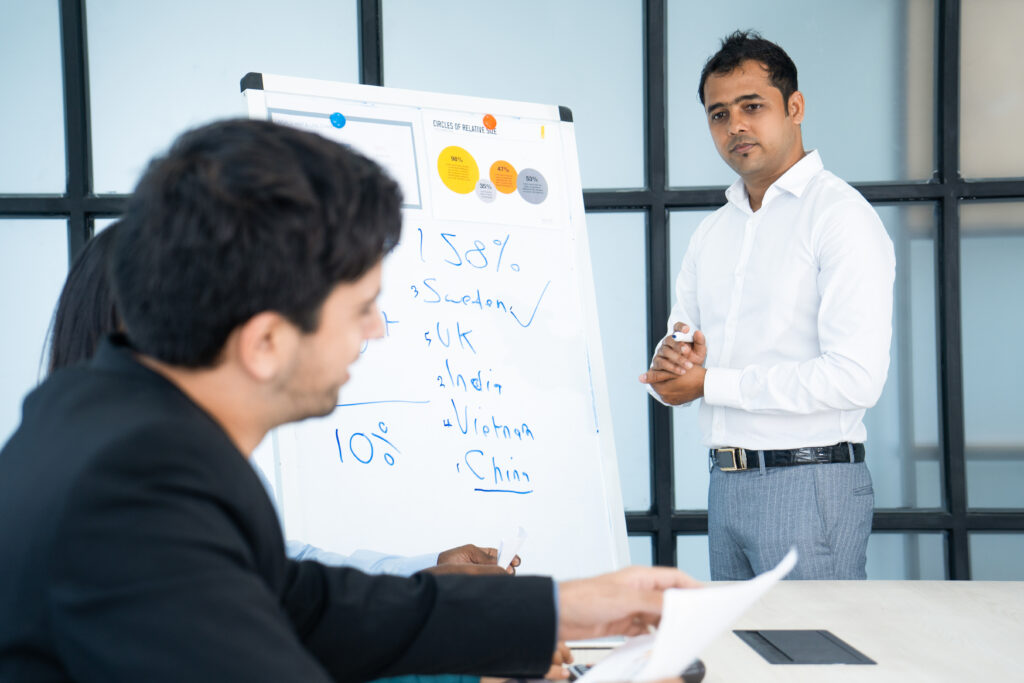
Quality Management Systems (QMS) like ISO 9001 are more than just certificates on a wall—they are the backbone of consistent performance, customer trust, and operational excellence. At the core of a thriving QMS lies one often underestimated element: continual training. No matter how comprehensive your system is, it is only as effective as the people managing it.
Throughout my decades working with maritime companies and small to mid-sized enterprises, I’ve seen the impact of ongoing training firsthand. Businesses that prioritize continual learning not only avoid stagnation but also elevate their standards. There is a direct link between continual improvement and business success, and training is the vehicle that is a key support in that journey.
Why Continual Training Matters in Quality Management
Keeping Up with Evolving Standards
ISO standards aren’t static. ISO 9001 itself has undergone several revisions over the years. Businesses that don’t train their teams regularly risk falling out of conformity. However this is not all that is evolving. Compliance obligations are evolving and as a result risks to the process which lead to changes to the process to mitigate these risks. The importance of quality management training becomes critical when standards evolve—because what worked yesterday may not satisfy today’s expectations. Further additional training such as FMEA and problem solving prove valuable assets in an employee’s skill set.
Addressing Changing Customer Expectations
Customer expectations today are higher and more fluid than ever. Continual training helps quality management teams adapt to these changes by enhancing their ability to identify trends, analyze feedback, and implement responsive changes. One client in the logistics sector updated its training modules and noted reduction in user errors.
Reducing Errors and Improving Consistency
Mistakes in quality management usually stem from a lack of awareness or understanding. In one engineering services company I consulted for, inconsistent recordkeeping was leading to frequent audit findings. After implementing training for ISO standards, non-conformance reports dropped by 40% within six months. Continual training instills consistency and reduces costly errors.
Core Areas to Focus on During Quality Management Training
Internal Audits
Effective internal audits are a pillar of any ISO 9001 system. Providing internal audit training empowers staff to identify gaps before external auditors do. For instance, a food packaging SME trained their department heads as internal auditors and saw a 50% reduction in minor non-conformities during certification renewal.
Risk Management
Modern QMS frameworks emphasize risk-based thinking. Employees should be trained in identifying, evaluating, and mitigating risks. Structured risk management training helps businesses anticipate disruptions and make data-driven decisions. A UK-based electronics firm credits their stable growth during Brexit to scenario planning introduced through risk-focused training modules.
Customer Satisfaction Improvement
Training teams to effectively track, analyze, and respond to customer feedback ensures that quality doesn’t just meet but exceeds expectations. One case in point is an IT services company that held quarterly feedback analysis training. Within a year, they saw customer complaint resolution time cut in half.
Document Control
Poor documentation can unravel an otherwise sound system. Proper training ensures that document management is consistent, accessible, and aligned with regulatory requirements. When a ship maintenance contractor implemented a document control training module, audit time was reduced by two days due to quicker access and better version tracking.
Benefits of Regular Training for Employees
Increased Employee Engagement
When staff feel invested in, they reciprocate through higher ownership and accountability. Employee training benefits include stronger morale and lower turnover. A maritime safety company I worked with reported a 25% drop in staff attrition after launching a quality-focused training initiative.
Improved Efficiency and Product Quality
Skilled employees waste less time and deliver higher quality outputs. A Swiss manufacturing firm using Lean principles alongside ISO 9001 saw productivity rise 20% after implementing skill-based development paths.
Higher Customer Satisfaction Rates
Customers notice when a business is responsive and consistent. Continual training enhances the service culture, as knowledgeable employees handle queries and issues more effectively. Improved quality leads directly to happier customers.
Best Practices for Implementing Continual Training Programs
Regular Workshops and Refresher Courses
Schedule recurring workshops to ensure that staff stay updated. These can be quarterly or semi-annual, based on system complexity. One health care distributor holds monthly ISO huddles and credits it with their 98% audit readiness score. This also helps build memory muscle and increase knowledge retention.
Online Training Platforms
Digital learning tools are cost-effective and accessible. QMII has worked with clients to develop custom ISO 9001 training courses tailored to various industry needs. The elearning is an effective tool to develop blended with in-person workshop reinforcement.
Certification Renewals and Upgrades
Make sure employees know that training doesn’t end with initial certification. Renewal cycles often introduce updates, and staff must be prepared. Invest in quality management training programs that include updates on ISO revisions and emerging practices.
Tools and Resources for Quality Management Training
- Online Courses: Contact QMII to learn more about how we can develop custom eLeaning modules for your organization. We also provide all our classes in a virtual instructor-led format.
- Webinars: QMII frequently host free webinars on trending QMS topics.
- Consultants: Working with experienced consultants accelerates learning and contextualizes standards for your business. QMII consultants are all field experienced and bring that experience to the classroom to enhance your learning.
Conclusion
Training isn’t an expense—it’s an investment in the stability and future of your QMS. A quality management system that is static soon becomes obsolete. Continuous improvement is only possible when learning is continual too.
Whether you’re aiming to reduce audit findings, improve product consistency, or boost customer trust, the answer often lies in a better-trained team. Don’t wait for non-conformities to force change.
Invest in continual training today and future-proof your quality processes for tomorrow.